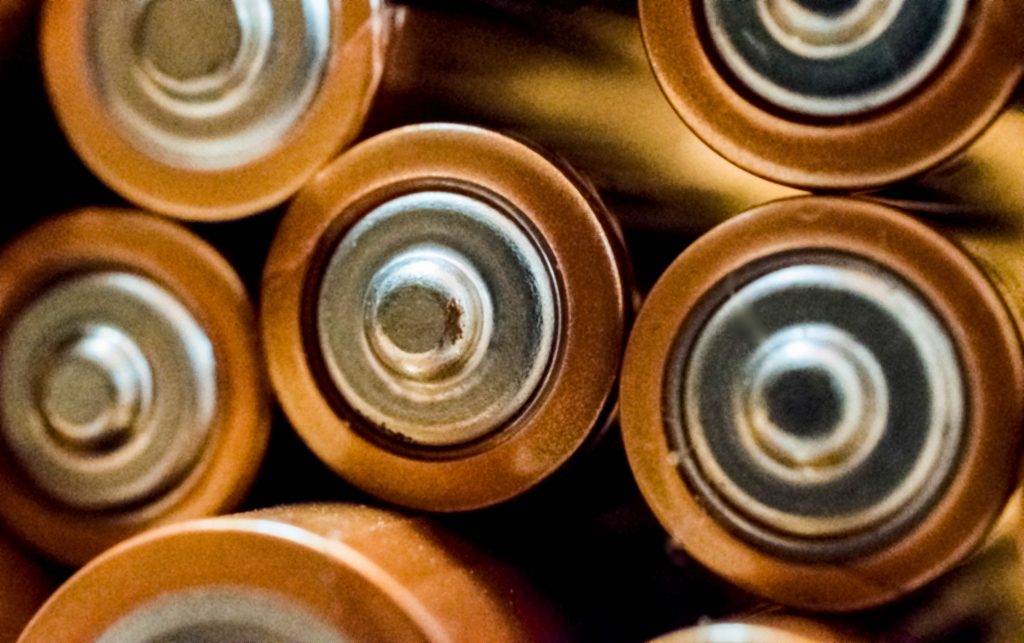
What is Deep Discharge? How To Build A Simple Battery Protection Circuit
Batteries you use in a variety of projects, from uninterruptible power supplies to remote-controlled cars, may be damaged by deep discharging. Learn about deep discharging and how to protect your batteries. Here you will find helpful terms and a simple circuit that can protect your battery-powered projects from malfunctioning.
What is Deep Discharging?
A deep discharge occurs when the capacity of a battery has been exhausted. Battery cells have a set voltage at which they cease to function. This voltage is called the cut-off point. Exhausting deep causes 1.5 to 2 times as much electric discharge as the battery can support. As a result of over-discharging, the battery will have increased internal resistance, making charging difficult. The price tag on these batteries is high.
Depth of Discharge
According to the Depth of Discharge chart, the battery has used a percentage of its capacity as compared to its total capacity. If the batteries’ full capacity is 15kWh and you discharge 12kWh, that’s 96%. As a result, a deep discharge is something you should avoid. A deep cycle battery is a battery that is designed for deep discharge regularly. Power storage, UPS, traffic signals, and remote applications use these batteries.
Deep Discharge Protection Circuits
Identification of the battery’s cut-off voltage is necessary for deep discharge protection. A Zener diode in reverse bias condition will act as an open circuit when its cathode voltage falls below the breakdown voltage. It starts conduction when the cathode voltage is above its breakdown voltage. A switch disconnects the load from the battery, thus disconnecting the battery from the device. When the batteries reach the cut-off voltage level, we need to design a circuit to turn on a switch.
Protection Circuit for 12V Batteries
We will build a protection circuit to protect the load and battery from over-discharging, we will build a protection circuit. To adjust the resistance to achieve the desired range of operation, we’ll use a similar circuit but change the resistance. The diode is no longer conduction and there will be no base voltage, which effectively disconnects the battery from the load when the voltage is below 8V. We hope to use this circuit to protect the battery and the load from overcharging.
ICs Used for Over-Discharge Protection
Cs make our work easier when we are dealing with a complex circuit and have to regulate the power for the load. It is possible to replace several circuits with one integrated circuit. Integral circuits are capable of simultaneously monitoring and controlling power flow. Two integrated circuits can handle this application.
The LTC2960
A high voltage multi-cell battery monitor, the LTC2960 IC provides two input voltages. If the battery voltage is low, the RST pin in the IC signals a low voltage by going high. A user can provide the IC with either inverting or non-inverting inputs. Portable battery-powered equipment, batteries, and other systems commonly use this IC.
The LT1495
LT1495s are low-power op-amps that are capable of delivering very low supply currents. The supply can be fitted to 3V, 5V, or +- 15V. With a voltage range of 2.2V-36V, this device makes it possible to regulate a wide range of voltages. This IC offers several advantages over other protection circuits, including the fact that the circuit made by the IC uses less than 4.5miliamps of current. The device also protects batteries up to 18V.
How to Charge an Over-Discharged Battery
When a battery is overcharged, its internal resistance increases. Battery capacity can be lost twice as a result of this, so the battery has a hard time being recharged. When the voltage drops below 3.0V, severe damage occurs. Check the battery periodically for heat buildup and do not leave it unattended. In this situation, charges can be reduced. During puffing or overheating, it is impossible to restore the battery. Charges from batteries follow a similar pattern.
If you’re looking for the best place to get your power supplies, you’re in the right place! EP-Power aims to give you a total commitment to ensure the best quality and provide first-class products and services.
For inquiries, you may send us an email at: sales@edac.com.sg or give us a call at +6564547877.